Flexibility – Diversity – Training
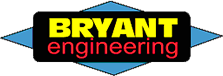
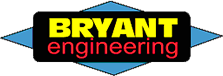
Flexibility – Diversity – Training
Our general engineering section operates in support of the the other sections and is there to provide a service to our customers by offering a “One Stop Shop Engine Machining Facility”
1. Assess Requirements
Let’s work out exactly what needs to be done.
2. Document a Plan
Everything is documented so nothing is missed.
3. Delivery
We’ll deliver your job in a reasonable time frame.
Fully Equipped Workshop
This Facility is designed to carry out repairs on all the ancillary equipment associated with an engine including Exhausts, Pump Shafts, Housings, Pulleys etc
Providing Solutions Since 1929
Facilities include:
Fully Equipped Workshop
This Facility is designed to carry out repairs on all the ancillary equipment associated with an engine including Exhausts, Pump Shafts, Housings, Pulleys etc
Providing Solutions Since 1929
Our facilities have everything that we need for big jobs and small and can handle almost any engineering requirement:
Frequently Asked Questions
Its a common question customers ask us, and there is no one simple answer. Even though we work with the same types of jobs frequently there can always be unforeseen circumstances that can take additional time. Once we understand the nature of your enquiry we will work with you to ensure there is a reasonable deadline set that meets your expectations.
Following the initial inspections a report and quotation is prepared.
Why Choose Us
Other Services
cylinder blocks
Machining blocks with a bore size from 50mm – 250mm, lengths up to 3300mm and weights up to 3000kg
crankshafts
Handling crankshafts with a maximum length of 4000mm, weight up to 2000kg and a maximum stroke of 420mm
component cleaning
Our Ferrous tank handles items up to 3000mm long & 2500kg, we also have a modern ultrasonic non-ferrous cleaning system and a dedicated oil cooler ultrasonic cleaning system
con rods
We can handle up to a maximum tunnel bore of 200mm and use induction small end eye heating for bush fitment
cylinder heads
Our facilities include a CNC valve Seat Cutter, stainless steel injector tube replacement tooling and a temperature controlled pressure tester